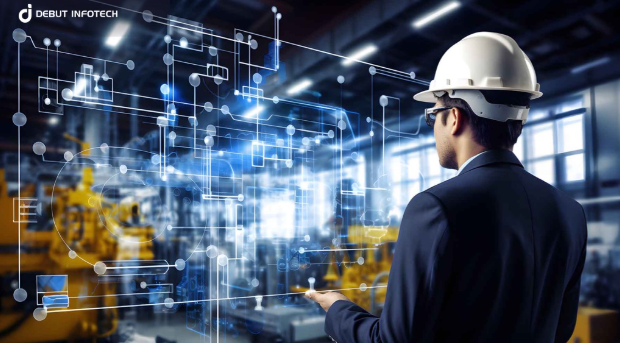
Technology has transformed how businesses run their operations in today’s fast-paced sectors, boosting efficiency and cost savings. One area where this change is incredibly clear-cut is AI in predictive maintenance. To prevent equipment failures from interrupting operations, this unique solution uses cutting-edge technologies to foresee potential equipment failures.
Artificial intelligence can enable companies to go from conventional repair techniques to more smart, data-driven ones. The proactive predictive maintenance approach minimizes downtime and maximizes resource efficiency, saving both time and money.
What Is Predictive Maintenance?
Predictive maintenance is the process of keeping an eye on the state and performance of equipment to detect problems before they happen. Predictive maintenance uses real-time data to forecast when a machine could fail, unlike reactive maintenance—which only tackles problems once they arise—or preventative maintenance—which depends on planned servicing. This method prolongs equipment life and helps to decrease unanticipated breakdowns.
Artificial intelligence (AI) applications have sped up the processing of massive amounts of data, which has completely changed predictive maintenance. Together, sensors, IoT devices, and AI models deliver helpful information that guarantees quick actions and lowers running hazards.
How AI Enhances Predictive Maintenance
By providing practical information and raising operational efficiency, AI applications in predictive maintenance have changed how companies approach equipment management. Large volumes of IoT device and sensor data processed at lightning speed by artificial intelligence expose trends and connections that are sometimes undetectable to the human eye. These revelations provide precise forecasts of equipment condition and enable companies to respond early, reducing disruption and optimizing output.
Here are some key ways AI is redefining predictive maintenance:
1. Fault Detection and Diagnosis
AI systems are highly effective at identifying potential flaws with equipment at an early stage. Artificial intelligence models can find anomalies suggesting possible problems by examining vibration, temperature, or pressure sensor data. For instance, people might not detect slight variations in machine performance, but AI models can spot them immediately and allow maintenance personnel to fix issues before they become more serious. Employing proactive issue identification minimizes unplanned downtime and avoids expensive repairs.
2. Predictive Analytics
Predictive analytics is among the most potent AI use cases in predictive maintenance. Learning from historical and real-time data will help artificial intelligence precisely project equipment performance over time. This lets companies schedule maintenance based on well-predicted failures far in advance. With accurate predictions, businesses can use data to make choices that improve the reliability of their equipment and make operational planning easier.
3. Optimizing Maintenance Schedules
Conventional approaches to maintenance depend on set timetables, which could result in pointless servicing or neglected problems. With the help of AI integration, this can be changed by making maintenance schedules that adapt to the actual state of the equipment. Constantly analyzing data, AI-driven solutions guarantee that maintenance activities are carried out just when necessary. This method guarantees machines run at maximum performance levels, saves time, and helps to lower unneeded expenses.
4. Remote Monitoring
AI development services let companies keep an eye on machinery remotely. AI-powered platforms receive real-time data from connected devices and analyze it to conclude. This information is available to maintenance teams from anywhere, so they don’t have to go to the spot to check it out. This lets them respond more quickly to potential problems. Managing geographically scattered assets or equipment at difficult-to-reach sites calls specifically for remote monitoring.
5. Improved Resource Allocation
Artificial intelligence systems maximize resource allocation efficiency by pinpointing each machine’s maintenance requirements. This guarantees efficient use of tools, labor, and spare components, lowering running expenses and waste. AI can also assist in prioritizing necessary maintenance chores and focus on equipment most likely to develop issues.
Companies increase equipment dependability and generate fresh degrees of efficiency by including these modern features in their activities. Advances in AI technology will make predictive maintenance in AI even better, helping companies stay competitive in an industry that is changing quickly.
The AI Tech Stack for Predictive Maintenance
AI predictive maintenance calls for a strong AI tech stack. These are the main elements:
- IoT Devices and Sensors: Among other vital data, these instruments gather vibration, pressure, and temperature.
- Data Processing Tools: Effective operation of artificial intelligence models depends on vast amounts of orderly structured data. Data processing and organization tools like Apache Kafka or cloud platforms handle this task.
- Machine Learning Algorithms: AI development companies design machine learning algorithms tailored for predictive maintenance. These algorithms analyze data and provide actionable insights.
- Cloud Computing: Cloud Computing solutions provide rapid and efficient forecasts by storing data and enabling AI applications to scale naturally, ensuring ease.
- Visualization Tools: AI-integrated dashboards enable businesses to see equipment health and spot trends.
Real-World AI Applications in Predictive Maintenance
Predictive maintenance in AI has changed the way industries function and has several uses in different fields:
- Manufacturing: Predictive maintenance driven by artificial intelligence guarantees flawless manufacturing by tracking equipment for wear and tear. By analyzing real-time data, advanced sensors, and AI models flag problems before they affect manufacturing lines. This lowers waste, increases operational efficiency, and lessens unscheduled downtime, resulting in a simpler meeting of production targets and cost control.
- Energy Sector: Turbines, power grids, and pipelines are essential infrastructure for the energy industry. Artificial intelligence uses predictive analytics to detect minute performance irregularities, such as temperature variations or pressure fluctuations, indicating possible breakdowns. By acting quickly on these insights, we can ensure the energy supply stays on and avoid expensive outages or environmental hazards.
- Automotive: AI has revolutionized automotive maintenance by allowing systems to identify component wear and tear, including those of engines, tires, and brakes. Predictive maintenance generally enhances the driving experience, reduces breakdowns, and increases vehicle safety. AI applications are now included in automakers’ manufacturing facilities to track assembly lines and maximize vehicle production.
- Healthcare: In healthcare, patient results depend much on the dependability of medical tools and equipment. AI integration lets clinics and hospitals track equipment, including surgical tools, ventilators, and MRI scanners, for possible problems. Predictive maintenance guarantees these gadgets operate without malfunction, preserving high treatment standards and life protection.
These practical artificial AI use cases show how artificial intelligence is transforming operations, helping businesses prevent failures and save money while maintaining output by avoiding mistakes. Predictive maintenance is becoming non-negotiable in modern corporate operations as its adoption rises.
Benefits of AI in Predictive Maintenance
Using AI in predictive maintenance has advantages for many sectors beyond operational enhancement to lower risks. Principal benefits include:
- Reduced Downtime: Predictive maintenance driven by AI applications helps to lower unexpected outages by early identification of possible problems. Constant monitoring guarantees that equipment keeps running, increasing output and reducing disruption of processes.
- Cost Savings: Taking care of minor issues before they become significant failures can help you save a lot of money. Businesses save money and keep seamless operations by lowering the demand for emergency repairs, replacements, or lengthy downtime.
- Improved Safety: Predictive maintenance in AI helps employees avoid dangerous circumstances by spotting any breakdowns beforehand. Early warnings regarding structural flaws in heavy machinery, for instance, can save workers injuries and lives.
- Longer Equipment Lifespan: Condition-based monitoring, an essential AI use case, ensures that machines operate under optimal conditions. Timely maintenance extends the lifespan of equipment, reducing the need for frequent replacements and maximizing return on investment.
- Better Resource Allocation: By concentrating on high-priority activities, companies can simplify maintenance processes using AI development services. By focusing their time and resources on equipment requiring maintenance instead of regular checks, maintenance personnel help to increase general efficiency.
The Future of AI in Predictive Maintenance
In predictive maintenance, artificial intelligence has quite bright prospects. Companies will have access to more advanced equipment monitoring and management solutions as artificial intelligence technologies develop. Trends in the future of AI include:
- Advanced AI Models: Enhanced machine learning algorithms can predict failures more accurately.
- Autonomous Maintenance Systems: Fully automated systems that can predict failures and perform minor repairs.
- AI Development Services: There is a rise in specialized AI development companies offering tailor-made solutions for predictive maintenance.
- Integration with Robotics: Robots powered by AI will soon be able to conduct physical inspections and repairs, further improving efficiency.
How Debut Infotech Can Help Businesses
You can rely on Debut Infotech as a reliable partner when implementing AI in predictive maintenance. Being among the top artificial intelligence development companies, our area of expertise is creating innovative ideas catered to your particular requirements.
Custom AI development services catered to your particular equipment and operational needs allow Debut Infotech to guarantee the best performance and efficiency. Our team guarantees flawless AI integration by matching solutions with your current systems, allowing a hassle-free shift to artificial intelligence-driven maintenance. Knowing predictive analytics, we assist in maximizing production, reducing downtime, and optimizing maintenance plans. Furthermore, we offer a strong AI tech stack that guarantees your predictive maintenance solution is efficient and future-ready via end-to-end support from IoT sensor setup to cloud-based data processing.
You gain access to state-of-the-art technologies and a team committed to driving your business forward with AI innovation by choosing Debut Infotech.
Conclusion
Artificial intelligence has become a game-changer for predictive maintenance, allowing companies to go from reactive to proactive management. Using artificial intelligence in predictive maintenance can help businesses reach operational excellence, lower expenses, and increase safety. The potential applications of AI are practically limitless, whether one considers sophisticated AI models, predictive analytics, or strong AI integration. Working with AI development firms such as Debut Infotech guarantees you have the most excellent tools for implementing artificial intelligence in maintenance and beyond.